In-Mold Decorations Demystified: Opening the Keys Behind This Advanced Manufacturing Process
In today's hectic manufacturing landscape, in-mold designs have emerged as an innovative strategy that proceeds to intrigue market specialists. Stay tuned as we dissect the underlying concepts and introduce the enigmatic appeal of in-mold designs, shedding light on the secrets that thrust this process to the forefront of modern production methodologies.
The Advancement of In-Mold Decorations
The advancement of in-mold designs has been marked by substantial improvements in modern technology and style development. In-mold decors were limited in their intricacy and color options. Nonetheless, with the introduction of new production strategies and materials, the opportunities have increased tremendously.
One secret advancement has been the growth of high-resolution printing processes that permit detailed styles with dynamic shades to be transferred onto items during the molding process. This has actually enabled makers to achieve photorealistic pictures and thorough graphics that were previously unattainable.
In addition, the combination of robotics and automation in the in-mold decor process has actually boosted efficiency and consistency in using decorations to products. This not just lowers production time yet additionally enhances the general top quality of the finished products.
Comprehending the In-Mold Refine
Marked by considerable advancements in innovation and style technology, the evolution of in-mold designs has actually led the way for a deeper understanding of the complex procedure involved in producing these ornamental components. The in-mold procedure is a sophisticated manufacturing technique where ornamental components are incorporated straight right into the end product during the molding process. This technique involves placing a pre-designed decoration, such as a graphic or label, into the mold cavity before injecting the material. As the material streams into the mold, it bonds with the design, leading to a seamless combination of the design into the product.
Comprehending the in-mold process calls for exact control over different parameters, including timing, temperature, and stress, to make certain the design adheres effectively to the product. In addition, choosing the right products is important to achieving high-grade results. By understanding the ins and outs of the in-mold process, makers can produce visually striking items with durable, durable designs that boost both the appearances and performance of the end product.
Benefits of In-Mold Decorations
Progressing item aesthetic appeals and resilience, in-mold decors offer a structured strategy to integrating ornamental aspects throughout the manufacturing process. Among the key benefits of in-mold decors is the smooth integration of graphics, textures, and shades directly right into the item throughout the molding procedure. In-Mold Decorations. This gets rid of the demand for post-production webpage design techniques, such as painting or printing, which can be lengthy and expensive
Additionally, in-mold designs are very sturdy as the graphics are enveloped within the item, making them resistant to wear, scratches, and fading. This leads to products that preserve their aesthetic charm and branding for a longer duration, even in rough settings.
Along with enhancing aesthetics and sturdiness, in-mold designs likewise use increased style versatility. Makers can quickly integrate complex styles, structures, and branding aspects that would be difficult or tough to attain with standard design techniques.
Applications Across Industries
Throughout various markets, in-mold my company decorations have discovered functional applications that enhance both the visual charm and durability of products. Furthermore, the home appliance sector makes use of in-mold decorations to produce elegant and durable control panels and fascia for products like stoves and refrigerators. Generally, in-mold decors supply a cost-effective and efficient method to enhance the aesthetic appeals and longevity of items throughout a vast array of industries.
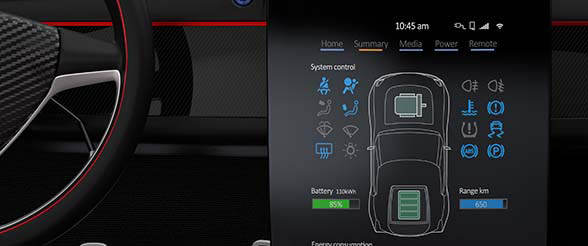
Future Patterns in In-Mold Innovation
The development of in-mold decorations is poised to proceed shaping the landscape of item design and production as Future Trends in In-Mold Technology guarantee cutting-edge solutions to further improve aesthetic aesthetic appeals and item sturdiness. In addition, developments in electronic printing techniques are allowing suppliers to accomplish better customization and detail in in-mold designs, opening up brand-new possibilities for innovative item designs. One more considerable pattern is the assimilation of smart innovations, such as NFC tags or LED illumination, straight right into in-mold decorations, adding practical and interactive aspects to items.
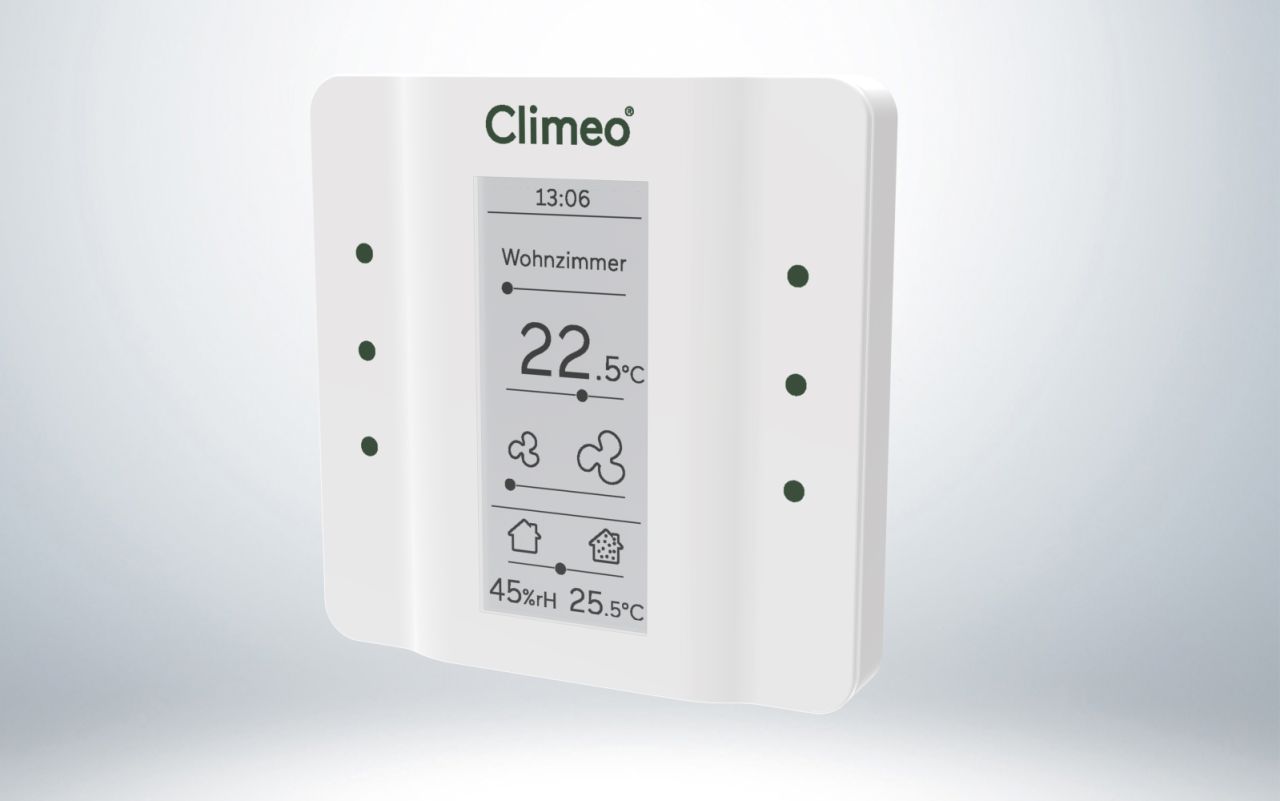
Conclusion
In-mold designs have reinvented the production procedure by effortlessly incorporating style elements into items. With its various benefits and versatile applications across various industries, in-mold technology check this is positioned to proceed shaping the future and progressing of production.
By grasping the complexities of the in-mold process, producers can produce visually striking items with long lasting, resilient designs that improve both the looks and performance of the final product.
Progressing item aesthetic appeals and sturdiness, in-mold decorations offer a structured technique to integrating decorative components throughout the manufacturing process. One of the vital benefits of in-mold decorations is the smooth combination of graphics, textures, and shades straight into the item during the molding procedure.The development of in-mold decorations is positioned to continue forming the landscape of product layout and manufacturing as Future Trends in In-Mold Modern technology guarantee innovative options to even more boost visual appearances and product durability.In-mold designs have reinvented the production process by seamlessly integrating layout elements right into products.
Comments on “In-Mold Decorations: Integrating Style and Manufacturing Excellence”